Musk Is Giving Up On Tesla's Biggest Advantage
It seems like a bananas move, but it actually makes sense. At least to Musk.
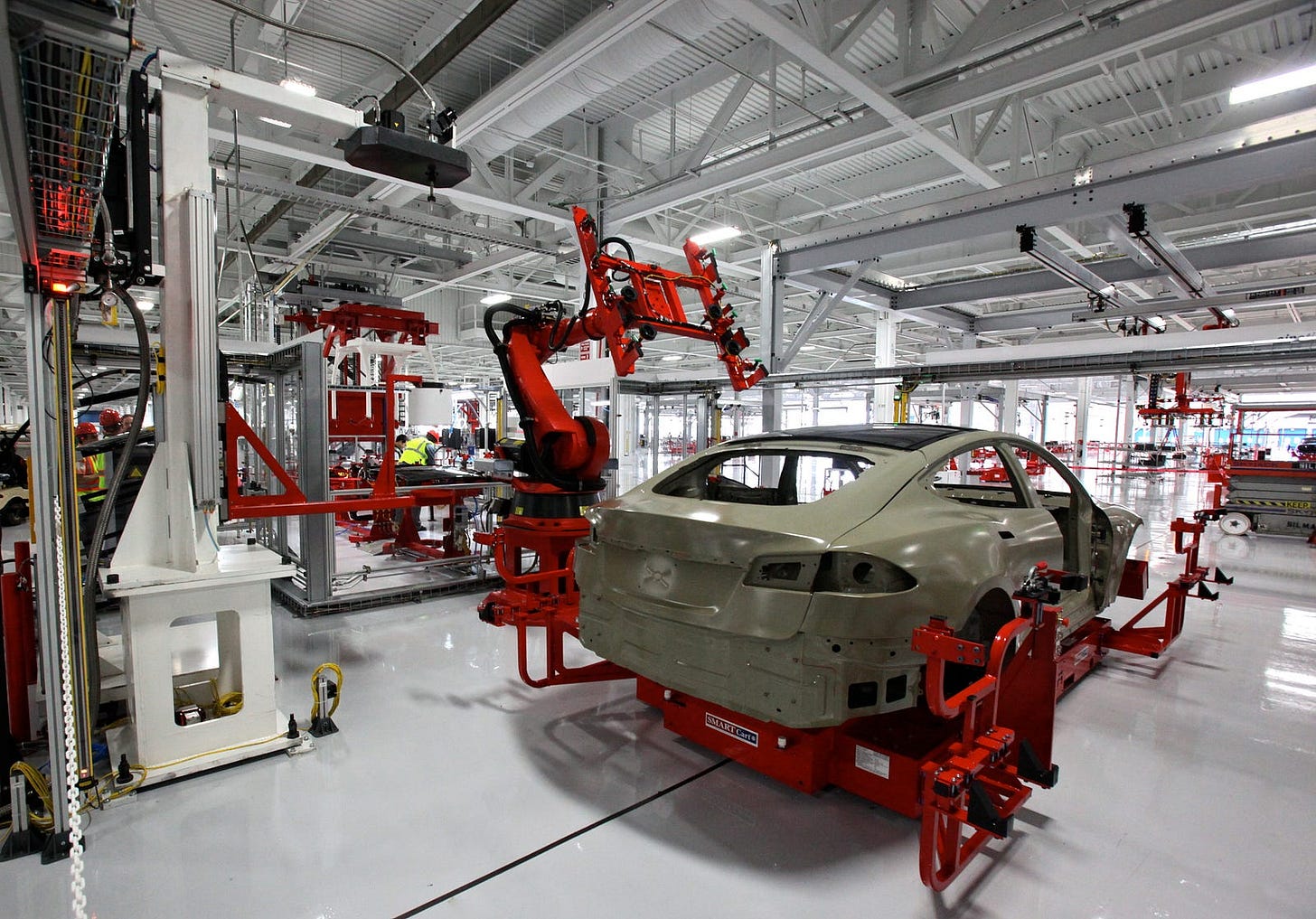
What is Tesla’s biggest industry advantage? Is it self-driving AI? It’s charging network? It’s in-house 4680 battery? Well, there is actually a good argument that it is actually gigacasting. This innovative technology allows Tesla to build a chassis far quicker and cheaper than any other automaker. In fact, Tesla claims gigacasting alone reduces the cost of producing a chassis by 40%! It’s thanks to gigacasting that Tesla was once one of the most profitable car companies on the planet, and how they have been able to slash the price of their vehicles over the past few years without totally wiping out their profits. In fact, gigacasting has been so successful for Tesla that the rest of the industry is now scrambling to catch up and implement this same technology. So it came as a huge surprise when, a few days ago, Reuters reported that Tesla had dropped their plans to take gigacasting to the next level. So, why has Musk done this? And will this harm Tesla?
Let’s quickly recap what gigacasting actually is.
Despite what you might have heard, Tesla didn’t invent gigacasting. They were merely the first to adopt it. The idea is to make the chassis production far more simple and cheaper. Regular car chassis are effectively a 3D puzzle of welded-together shapes stamped out from metal sheets. As you can imagine, this process is arduous and lengthy. In contrast, Gigacasting uses casting machines to force molten metal into moulds under high pressure to produce large aluminium body parts and, in some cases, entire sections of the frame. Casting such huge parts with high enough quality and tolerance levels to be automotive-grade is incredibly difficult. As such, these casting machines use thousands of tonnes of pressing force to ensure the molten metal fits and forms to the mould perfectly, hence the name “giga”.
Tesla currently uses gigacasting to produce the front and rear sections of the Cybertruck, Model 3 and Model Y chassis, with an aluminium and steel frame midsection holding the two together, completing the underbody of the chassis. But why? Well, it is significantly quicker than welding, and as this chassis fabrication stage is a production bottleneck, speed improvements here can dramatically speed up the entire production line. This, in turn, means a factory can be way more efficient. Gigacasting is also far more automated than welding, reducing the number of highly trained staff required and significantly reducing operating costs. This automation also allows for greater scaling flexibility, as it doesn’t cost loads to have the machine running slower or faster. All of this combined means the cost to produce a chassis using gigacasting is significantly lower than that of a welded one. As I said, Tesla claims this reduces their costs per chassis by 40%! However, other sources report it to be more like 20%-30%.
Tesla did plan to take this even further and gigacast the entire underbody in a single piece. This would require even more development and refinement to ensure parts met tolerance specifications, but in theory, it could reduce the chassis cost even more and increase factory efficiency significantly. In fact, this single unibody design was a core part of the upcoming budget Model 2 Tesla, as the drop in production costs would enable the $25,000 EV to turn a profit even at that low price. However, it would have undoubtedly made all of Tesla’s other models cheaper to produce, too.
But, a recent report by Reuters detailed two sources that claimed Tesla had decided to scrap these plans and keep its current three-piece underbody method. Why?
Well, Tesla has scrapped its Model 2 vehicle in favour of a self-driving robotaxi based on the same platform. A robotaxi doesn’t need the same ultra-low-cost production methods as a budget mass-market EV, and so the need for gigacasting the underbody in a single piece is less pressing. Tesla’s other models aren’t as dependent on this innovation, so scrapping won’t impact them too much, at least in the short term. What’s more, the costs of gigacasting are front-loaded. It is incredibly expensive to develop, refine and deploy, but over the long run and at scale, it works out cheaper per unit produced. Tesla is currently in the midst of a sales and profit catastrophe, and as such, it is desperately and dramatically cutting short-term spending to alleviate this issue. With the Model 2 gone, expensive gigacasting development could now be scrapped, along with a tonne of other costly programs, staff and core talent, helping Tesla save money.
But, it looks like short-term thinking might come back to bite Tesla.
Almost all of Tesla’s rivals are rapidly adopting gigacasting. Mercedes, VW, GM, Hyundai, Volvo, Toyota, and even Chinese rivals like BYD are all either currently using gigacasting or will in the next year or two. However, these manufacturers are looking to take gigacasting further than Tesla. Take Toyota, for example; they are proposing to unicast their EVs’ entire chassis (not just the underbody) by the end of the decade. This, combined with their upcoming solid-state 745-mile battery that is projected to cost less than current battery packs, could put them light years ahead of Tesla. But it isn’t just Toyota looking into this; BYD, GM and VW are all looking to do the same and have similar in-house battery development programs.
As such, over the next five years, we could see Tesla’s rivals leapfrog the once-dominant EV maker as they take gigacasting to the next level while Tesla’s development stagnates. This alone would be enough to make these rivals cheaper or more profitable than Tesla vehicles. However, with their in-house battery programs, these next-gen EVs could also have significantly better ranges and charge times.
So why has Musk shot himself in the foot like this? Well, it seems Musk has abandoned any plans to retain or expand Tesla’s dominant position in the EV market. Instead, he is entirely refocusing Tesla on unlocking fully self-driving cars. However, as I have mentioned before, not only will this be extremely expensive, requiring him to run the rest of Tesla extremely lean, but there is no guarantee that this will pay off. There is a good chance the AI might not improve enough, even with the levels of expenditure, training and refining Musk is planning. Even if it does, Tesla still has a huge Achilles heel, as they only use cameras to understand the world around them rather than using an entire suite of sensor types, leaving the system open to catastrophic misinterpretations. So, at least from where I am standing, it seems like Tesla is going to suffer significantly as its core business falls to the wayside as its competitors leapfrog Tesla and Musk tries to chase a rainbow.
Thanks for reading! Content like this doesn’t happen without your support. So, if you want to see more like this, don’t forget to Subscribe and follow me on BlueSky or X and help get the word out by hitting the share button below.
Sources: Reuters, Quartz, The Drive, Will Lockett, Will Lockett, Planet Earth & Beyond, Planet Earth & Beyond, Planet Earth & Beyond