Toyota Is Adopting Tesla's Most Controversial Design Feature
Cars might become a lot more disposable.
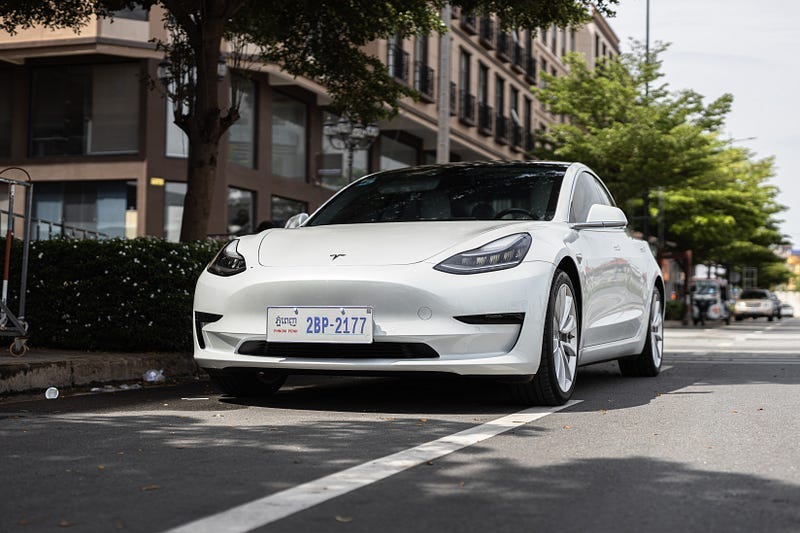
There are many reasons for Tesla’s domination of the EV world, such as its unique battery technology, widespread charger network and industry-leading efficiency. But the real secret sauce behind their success is a far more controversial and mostly uncovered piece of technology they have pioneered for the past six years. It has enabled Tesla to slash production costs, create industry-leading profit margins, and expand more rapidly than any other automaker. But, it also leaves their cars vulnerable and potentially less sustainable. However, despite these disadvantages, other auto industry giants, like Toyota, are now rapidly adopting this technology to compete with Musk. As such, it seems the world is about to switch to gigacasting.
You have probably already heard of gigacasting. It is a production method pioneered by Tesla and their partner Idra Group. It follows the same ethos as every other Tesla innovation: simplify design and reduce production costs.
** Quick interruption, if you want more from me, or interact with me, go follow me on Bluesky**
The idea is to produce complex parts of the car’s chassis, namely the front and rear sections, in one go rather than having to weld multiple pieces together to form the same part. You see, the complex shapes of the chassis around the wheel wells and suspension points are hard to make. So manufacturers usually use a simple cut-and-weld technique to build these 3D shapes from multiple 2D shapes. This production method is easy to design and set up, but it takes longer to make and is more expensive per part.
Instead, Tesla’s gigacasting technique revolves around a machine known as a giga-press. These high-pressure aluminium alloy casting machines are the only ones capable of producing such large 3D parts to high enough tolerances and without too many flaws. They press two dies together with a force of 6,000 tons, and a molten aluminium alloy is injected into the mould at a pressure of 20 bar. Once the piece has cooled and solidified, it is removed by a robot arm, the casts are cleaned, and another part can be cast. This entire process can take only 45 seconds! Now, these giga-press machines are not cheap at all and take a long time to set up. But once up and running, they can produce parts faster and cheaper than the cut-and-weld method.
Tesla has slowly adopted gigacasting in its factories since 2020. This means we can accurately compare these two chassis production methods, and the differences are staggering!
The Model Ys being built at Tesla’s Fremont factory use gigacasting for their front and rear chassis components. Compared to an older Model 3 (which uses the same chassis) that was built using the cut-and-weld method, these two castings replace 171 parts, negate 1,600 welds and remove 300 robots from the assembly line.
So what are the benefits of this? Well, Tesla claims this reduces their costs per chassis by 40%! However, other sources report it to be more like 20%-30%, so it is hard to tell if Tesla’s claim is yet more Musk bulls**tery. What isn’t exaggerated is the output speed, as this technology is one of the major reasons Tesla can build a Model Y in only 10 hours! This helps Tesla produce more vehicles from smaller, cheaper factories and meet their growing demand. These cast parts are also dramatically lighter than cut-and-weld parts, which helps Teslas accelerate faster and extend their range. In the right conditions, gigacasting can also create less material waste and use less energy, making it more eco-friendly.
Musk, being Musk, wants to take this technology even further. He wants to cast the entire chassis in one go. Unicasting like this would require giga-presses far larger than any before and a lot of refining to get it working smoothly. But if Musk can pull this off, it promises to enhance safety, range and performance while dramatically reducing manufacturing and material costs even further.
But it isn’t just Tesla pushing for unicasting like this. Toyota recently demonstrated a chassis which used gigacasting for the rear third of the chassis. This part was made in only three minutes and replaces a chassis component typically made of 86 pieces, taking 33 steps to assemble over several hours. As such, it promises to give Toyota a similar cost advantage as Tesla. Toyota will use this gigacasting on EVs from 2026 onwards. They even proposed that future cars could use unicasting for the chassis at this event.
But it isn’t just Toyota looking into this. Mercedes, VW, GM, Hyundai and Volvo are all preparing to or already using gigacasting for parts of their chassis and are all talking about eventually using unicasting.
This all sounds like good news, doesn’t it? A wide variety of EVs will become far cheaper and easier to produce as this technology is adopted across the industry. But gigacasting has some huge drawbacks.
Firstly, it makes the card a lot less repairable. With an ordinary chassis, it can be repaired if the frame takes some light damage in an accident. A mechanic can simply remove the damaged part and easily weld in a new one. But, with gigacasting, this can’t happen, and instead, the entire cast part needs to be replaced. As such, minor accidents which should be repairable can write off a car like the Model 3, as the cost to replace a cast is massive! This problem gets even worse with unicast chassis.
Now, this doesn’t mean a Tesla can’t be rebuilt after a crash. Musk has stated that the crash absorption rails at the front of the car can be cut and replaced with a bolted part for collision repair. But most accidents cause damage to far more than just the crash absorption parts of the chassis, so this point is mostly moot.
This can make the cars far less sustainable. It can also make insurance and financing such a car more expensive. This also shows a worrying trend with Tesla and the whole auto industry being very anti-right to repair, which is a whole other topic in itself. In other words, gigacasting can make cars more disposable, which goes against many of the environmental principles we need to work towards.
There are also major quality issues with gigacasting. Casting such a large piece can lead to massive geometric defects, as different areas of the part cool and contract quicker than others, causing inbuilt stress and flexure. This is partially why the cast needs to be under such extreme pressure, as this can alleviate this issue, but it doesn’t solve it. As such, a vast number of gigacast parts are scrapped. There are rumours that Tesla only uses 10% of its gigacast parts, as the rest don’t meet tolerances. In 2018, a Tesla employee said that 40% of the parts coming from the giga-press needed rework before being installed into a car! As such, the tolerances and quality of a gigacast chassis are much lower than a regular one, leading to deviations in its geometry which can affect safety, drive quality and reliability.
This problem is amplified by joining methods. As gigacast parts can’t be spot-welded to the rest of the chassis, they require a workaround to be assembled. This can again lead to more geometric variations and a low-quality chassis.
This is why gigacasting is a controversial technology. Yes, it means a company can produce more EVs at a far lower cost, enabling us to transition away from carbon-belching internal combustion faster. But it also means these cars are far less repairable, and therefore less sustainable, and potentially far lower quality. In the era of combustion engines, this throwaway attitude would be acceptable, as most engines are only good for a decade or two of use before they are beyond repair. But thanks to an EVs reduced number of moving parts and modern battery technology, these new electric cars could last for decades and decades or over a million miles, making them far more sustainable. However, this longevity would be useless if the vehicle could be written off so easily, thanks to gigacast parts.
So, is this technology good or bad? I’m not so sure.
Thanks for reading! Content like this doesn’t happen without your support. So, if you want to see more like this, don’t forget to Subscribe and follow us on Google News and Flipboard and follow me on Bluesky, or hit the share button below.
Sources: The Drive, Light Metal Age, Auto News Europe, CNBC, Tesmania, Sunrise, Nikkei